Introduction
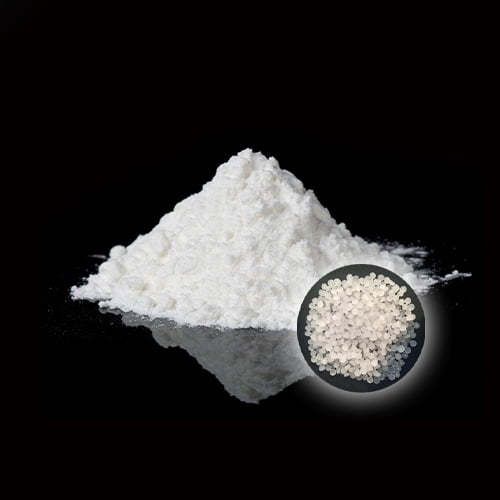
Polyvinylidene difluoride (PVDF) is a high-performance thermoplastic polymer known for its exceptional properties, including chemical resistance, thermal stability, mechanical strength, and electrical insulation. These properties make PVDF a versatile material with a wide range of applications in various industries, including chemical processing, electronics, construction, and medical devices.
Understanding Polyvinylidene Difluoride
PVDF is a type of fluoropolymer, which is a polymer containing at least one fluorine atom. It is derived from vinylidene difluoride monomer and is characterized by a carbon backbone with alternating fluorine atoms. This molecular structure endows PVDF with a variety of desirable properties that make it suitable for specialized applications.
Key Properties
- Chemical Resistance: PVDF can resist a wide range of chemicals, including acids, alkalis, and solvents.
- Thermal Stability: It has a high melting point and can withstand continuous use at temperatures up to 150°C.
- Mechanical Strength: PVDF exhibits high tensile strength and impact resistance.
- Piezoelectricity: It generates an electric charge in response to mechanical stress, a property utilized in sensors and actuators.
Applications of Polyvinylidene Difluoride in Modern Industry
Given its robust set of properties, PVDF finds itself at home in a diverse array of applications. Here are some of the key areas where PVDF is making a significant impact.
1. Aerospace and Automotive
PVDF’s chemical and thermal resistance make it ideal for aerospace components and automotive parts that are exposed to harsh environments.
2. Electronics
Its piezoelectric properties have led to its use in various electronic components, such as sensors, actuators, and energy harvesting devices.
3. Construction
PVDF coatings and films are used in building materials for their durability and resistance to UV radiation.
4. Chemical Processing
Its resistance to corrosive chemicals makes PVDF suitable for pipes, valves, and tanks in chemical plants.
5. Medical Industry
PVDF’s biocompatibility and chemical inertness make it a popular choice for medical devices and implants.
Comparative Analysis of Polyvinylidene Difluoride with Other Polymers
To further understand the advantages of PVDF, it is helpful to compare it with other commonly used polymers.
Polymer | Chemical Resistance | Thermal Stability | Mechanical Strength | Piezoelectricity |
---|---|---|---|---|
PVDF | High | High | High | Yes |
PTFE | High | High | Moderate | No |
Nylon | Moderate | Moderate | High | No |
PVC | Moderate | Low | High | No |
Production and Processing of Polyvinylidene Difluoride
The production of PVDF involves polymerization of vinylidene difluoride monomer, followed by processing into various forms such as films, sheets, tubes, and coatings. The processing techniques can affect the final properties of the material, making it crucial to choose the right method for the intended application.
Processing Techniques
- Extrusion: Used for producing tubes, profiles, and films.
- Molding: Suitable for creating complex shapes and components.
- Coating: Applied as a protective layer on various substrates.
Benefits and Challenges of Using Polyvinylidene Difluoride
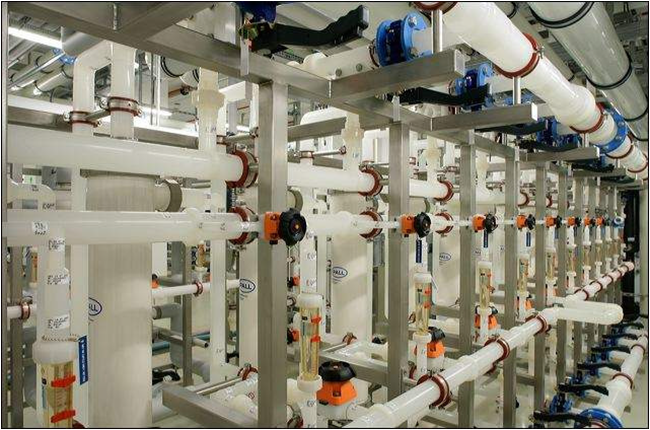
While PVDF offers numerous benefits, there are also challenges associated with its use.
Benefits
- Longevity: Due to its resistance to wear and environmental factors.
- Versatility: Its wide range of applications across industries.
- Safety: Inherent properties make it safe for use in sensitive environments.
Challenges
- Cost: PVDF can be more expensive than some alternative materials.
- Processing: Requires specialized equipment and techniques.
- Recycling: Limited recycling options due to its chemical resistance.
Conclusion: Polyvinylidene Difluoride
Polyvinylidene Difluoride, with its unique set of properties, has established itself as a key material in modern industry. Its applications are vast, ranging from aerospace and automotive to electronics and medical devices. As industries continue to evolve and demand materials that can withstand harsh conditions and perform reliably, PVDF is poised to play an even more significant role in the future.
FAQ
What are the primary advantages of using PVDF over other polymers?
PVDF offers a unique combination of chemical resistance, thermal stability, and electrical insulation, making it suitable for applications where other polymers might fail. Its durability and UV resistance also contribute to its advantages.
Can PVDF be recycled?
Yes, PVDF can be recycled. However, the recycling process is more complex compared to other plastics. Advances in recycling technologies are making it increasingly feasible to recycle PVDF efficiently.
Is PVDF safe for use in medical applications?
Yes, PVDF is biocompatible and is used in various medical devices and applications, including catheters and filtration membranes, due to its inertness and resistance to chemicals.
How does PVDF contribute to renewable energy solutions?
PVDF is used in the production of photovoltaic cells and lithium-ion batteries, where its stability and electrical properties enhance the efficiency and lifespan of these renewable energy devices.
What are some common products made from PVDF?
Common products made from PVDF include piping systems, wire insulation, chemical tanks, sensors, photovoltaic cells, and medical devices. Its versatility allows it to be used in a wide range of applications.